In recent years, with the continuous upgrading of environmental policies and the deepening of the “dual carbon” goal, industrial waste gas treatment has become the core issue of green transformation for enterprises. In this context, Kedil, with years of technical strength and rich project experience, has delivered an outstanding performance in a large container paint exhaust gas treatment project in Lianyungang.
The Lianyungang Container Spray Painting Waste Gas Treatment Project challenged a waste gas treatment air volume of 280000m ³/h and an initial concentration of 150mg/m ³. Through the efficient combination of “zeolite wheel+RTO process”, it successfully achieved comprehensive compliance with the emission standards for container spray painting waste gas treatment and passed the acceptance inspection, providing an innovative model for the green upgrade of container manufacturing industry. The challenge lies in the exhaust gas treatment air volume and initial concentration of 150mg/m ³. Through the efficient combination of “zeolite wheel+RTO process”, the comprehensive compliance emission of container spray painting exhaust gas treatment has been successfully achieved and accepted, providing an innovative model for the green upgrade of container manufacturing industry.
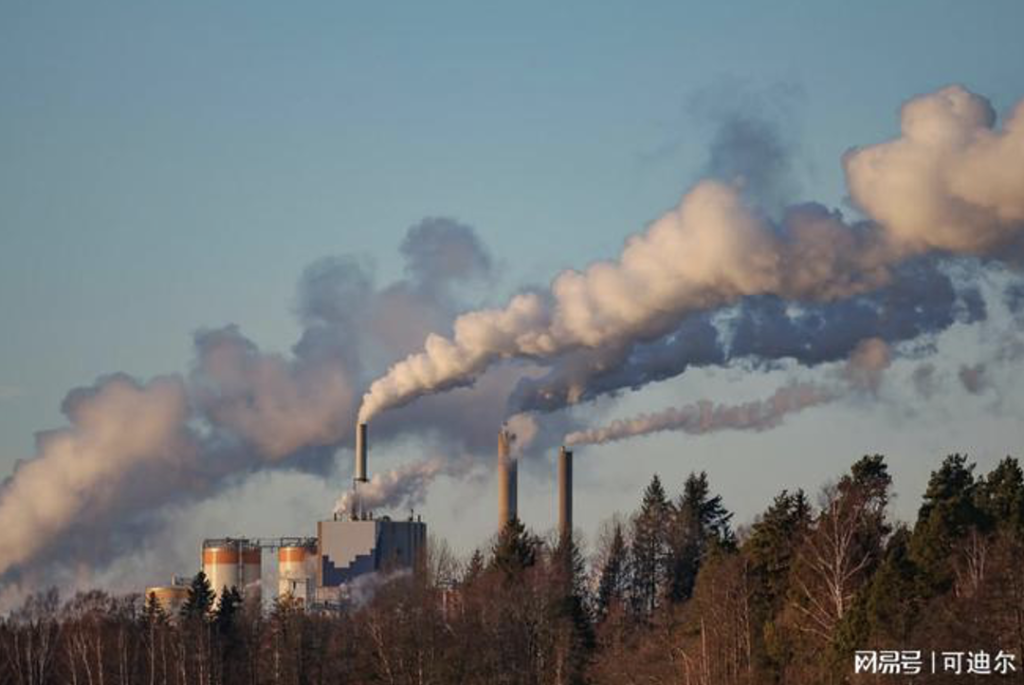
Project background: The treatment of exhaust gas from container painting is urgently needed
In the spray coating process of the container manufacturing industry, a large amount of volatile organic compounds and particulate matter are generated, mainly composed of propylene glycol monobutyl ether, isopropanol, ethylene glycol butyl ether, dipropylene glycol butyl ether, propylene glycol, etc. This type of substance not only poses a threat to the ecological environment, but also directly affects human health. As an important container production base in China, Lianyungang faces significant pressure in environmental governance. The original container spray painting exhaust gas treatment system of the enterprise is difficult to meet the strict requirements of Jiangsu Province’s “Comprehensive Emission Standards for Air Pollutants” (DB32/4041-2021) and “Emission Standards for Air Pollutants in Industrial Coating Processes”, and urgently needs to be upgraded and renovated.
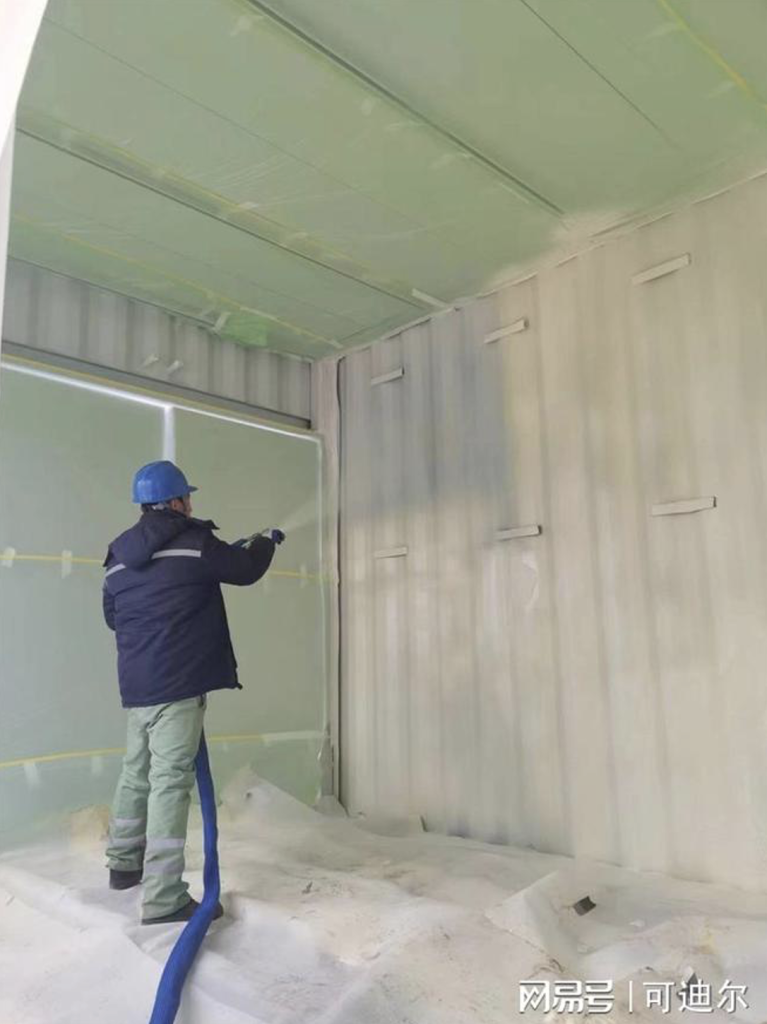
Technical Solution: Zeolite Wheel+RTO Efficient Combination Process
In response to the high air volume, multi-component, and low concentration exhaust gas characteristics of the project, the Kedil technical team has designed an integrated treatment solution of zeolite wheel concentration+RTO thermal storage combustion to assist in meeting the emission standards of container spray painting exhaust gas treatment. Fully leverage the synergistic effect of the two technologies.
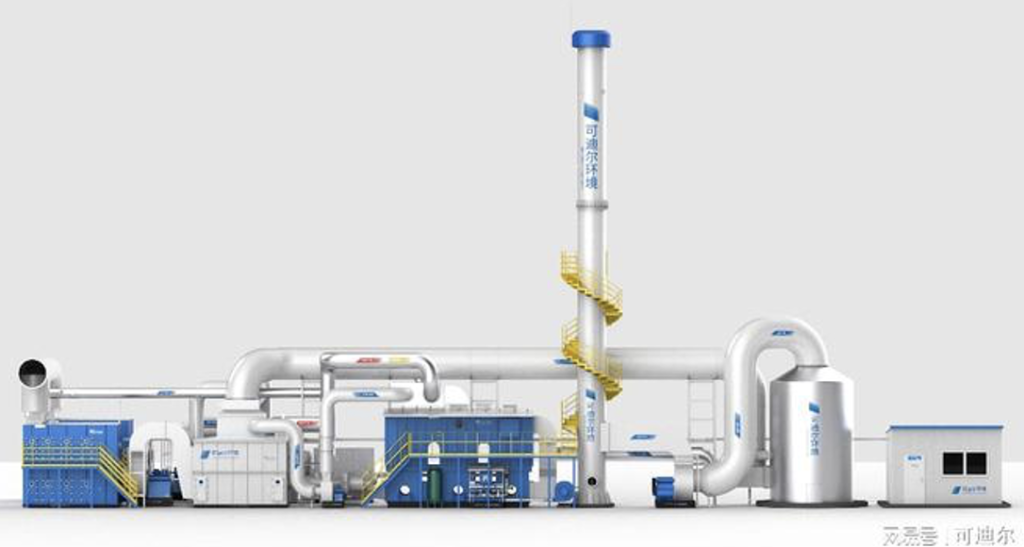
Zeolite wheel+RTO
Zeolite rotary adsorption concentration
By utilizing the efficient selective adsorption capability of zeolite molecular sieves, high air volume and low concentration exhaust gases can be concentrated to low air volume and high concentration states (concentration ratio can reach 10-30 times), significantly reducing subsequent treatment energy consumption.
RTO Thermal Storage Oxidation
The concentrated exhaust gas enters the RTO combustion chamber and is completely decomposed into carbon dioxide and water at temperatures above 760 ℃, with a purification efficiency of over 99%. The RTO system adopts a three chamber structure, which significantly reduces fuel consumption and achieves energy conservation and carbon reduction through the heat recovery of the thermal storage ceramic body.
Governance achievements: Emission indicators exceed national standards.
After third-party testing, the non methane total hydrocarbons and particulate matter in the treated container paint exhaust gas are ≤ 25mg/m ³ and ≤ 10mg/m ³, respectively. This not only meets the requirements of the “Jiangsu Province Comprehensive Emission Standards for Air Pollutants”, but also the “Emission Standards for Air Pollutants in Industrial Coating Processes”. The successful implementation of the container spray painting exhaust gas treatment project has reduced the annual emission of VOCs by over 300 tons for the enterprise, helped improve regional air quality, and reduced environmental compliance risks for the enterprise.

Project site
The successful acceptance of the Kedil Lianyungang Container Spray Painting Waste Gas Treatment Project confirms Kedil’s technological leadership in the field of complex working condition waste gas treatment. Its core advantages are reflected in:
Precise design: Customize adsorption oxidation process chain based on the characteristics of multi-component exhaust gas to ensure treatment efficiency and stability;
Energy saving and consumption reducing: The zeolite wheel concentration+RTO combination process saves more than 30% energy compared to traditional solutions;
Intelligent control: Integrated automation monitoring system, real-time optimization of operating parameters, reducing operation and maintenance costs.
Promote the upgrading of environmental protection throughout the entire industry chain
With the increasing global demand for environmental protection in container manufacturing, Kedil’s waste gas treatment technology has been successfully applied in multiple port cities and industrial bases. In the future, the company will continue to deepen its cultivation in the field of VOCs treatment and promote the development of zeolite wheels RTO、 The iterative innovation of catalytic oxidation and other technologies provides efficient and low-carbon solutions for more industries such as steel, chemical, and automotive coating, helping China’s manufacturing industry move towards a new stage of green and sustainable development.