Semiconductor manufacturing is the core industry of precision technology, but the exhaust gas generated during its production process is polluting. Improper treatment of semiconductor exhaust gas will threaten the ecological environment and human health. This article starts from the analysis of the sources of semiconductor exhaust gas, deeply interprets the necessity of governance, mainstream treatment processes, and shares the benchmark case of semiconductor exhaust gas treatment by Kedil in Shanghai, providing practical solutions for the industry.
1、Source of semiconductor exhaust gas
Semiconductor manufacturing involves key processes such as photolithography, etching, and cleaning, and exhaust gases are mainly generated in the following areas:
- Lithography and development: Clean the wafer with organic solvents such as acetone and isopropanol to release VOCs.
- Chemical vapor deposition (CVD): The reaction exhaust gas contains toxic gases such as silane and phosphine.
- Wet etching and cleaning: Acidic and alkaline solutions such as hydrofluoric acid and sulfuric acid evaporate to form sulfuric acid mist, hydrogen fluoride, and other acidic waste gases.
- Ion implantation and diffusion: Harmful gases such as ammonia and chlorine may be generated during high-temperature processes.
Typical exhaust gas composition:
Organic waste gas: acetone, isopropanol, butyl acetate, etc
Acid alkali waste gas: HF, H3PO ₄, H2SO ₄ mist, etc
Toxic gases: arsine, phosphine, etc. (requiring special treatment)
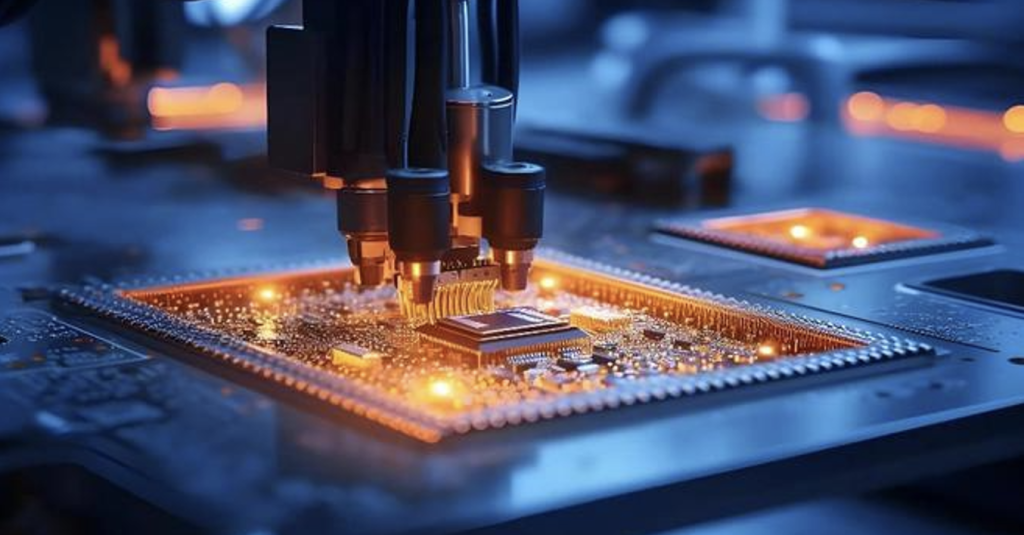
2、Comparison of mainstream processes for semiconductor exhaust gas treatment
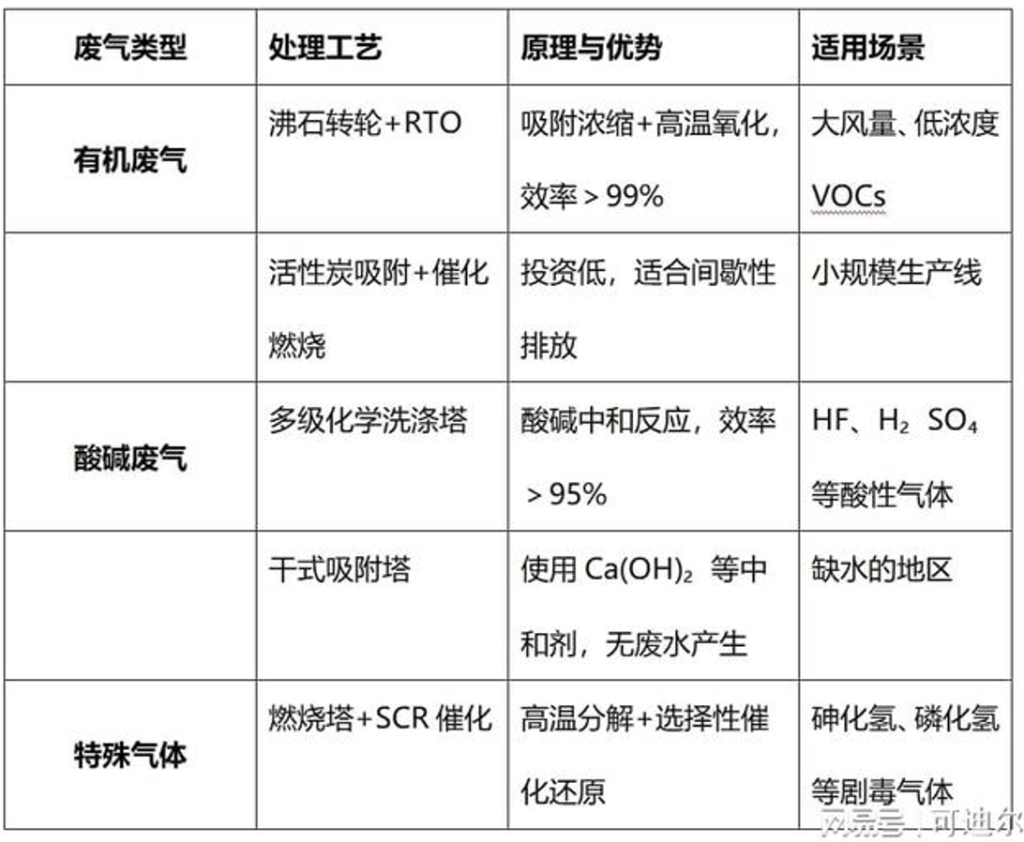
Industry trend: Zeolite wheel+RTO has become the preferred solution for semiconductor plant waste gas treatment due to its low energy consumption and strong adaptability.
3、 Semiconductor exhaust gas treatment case: practical case of Kedil Shanghai project
Background of Semiconductor Waste Gas Treatment Cases
Semiconductor factory exhaust gas treatment industry: semiconductor manufacturing
Location: Shanghai
Types of exhaust gases for semiconductor factory waste gas treatment:
Organic waste gas: air volume 33000m3/h, concentration 200mg/m3, containing acetone, isopropanol, etc
Acid alkali waste gas: air volume of 35000m ³/h, concentration of 20mg/m ³, containing sulfuric acid mist, hydrogen fluoride, etc
Semiconductor exhaust gas treatment plan
Kedil has designed a combination process of “zeolite rotary adsorption concentration+RTO thermal storage combustion” to treat organic waste gas based on the characteristics of semiconductor growth production lines; Acid alkali waste gas is treated using a scrubbing tower process, which removes substances such as sulfuric acid, phosphoric acid, and ammonia through acid-base neutralization, ultimately achieving the dual goals of efficient purification and energy conservation.
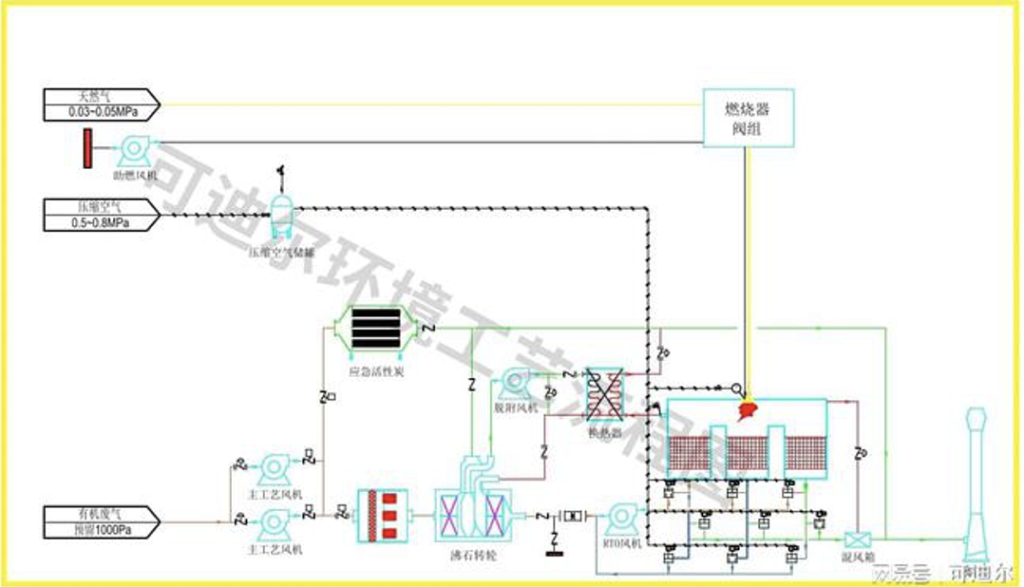
Zeolite adsorption efficiency ≥ 92%
Zeolite concentration factor: 25-30 times
RTO removal rate ≥ 99%
Semiconductor factory exhaust gas treatment results:
The processed non methane content is ≤ 20mg/m ³, and the emission indicators are superior to national and local standards. Currently, the system operates stably and efficiently.

3、 Why choose the Kedil waste gas treatment solution?
Industry experience: Serving over 300 semiconductor companies, familiar with the characteristics of process exhaust gases.
Technical advantage: Independently developed zeolite wheel material with strong resistance to high temperature and humidity.
Customized design: flexibly configure equipment according to workshop layout, saving floor space.
Intelligent operation and maintenance: remote monitoring system+regular maintenance services to ensure long-term compliance.
4、 Conclusion
The treatment of semiconductor exhaust gas needs to balance technical feasibility and economy. Through the combination process of zeolite wheel+RTO and chemical scrubbing tower, Kedil successfully achieved ultra-low emissions in the Shanghai semiconductor waste gas treatment project. If you need customized semiconductor processing solutions, please feel free to contact the Kedil environmental engineering team. We will provide you with one-stop services from testing, design to construction.
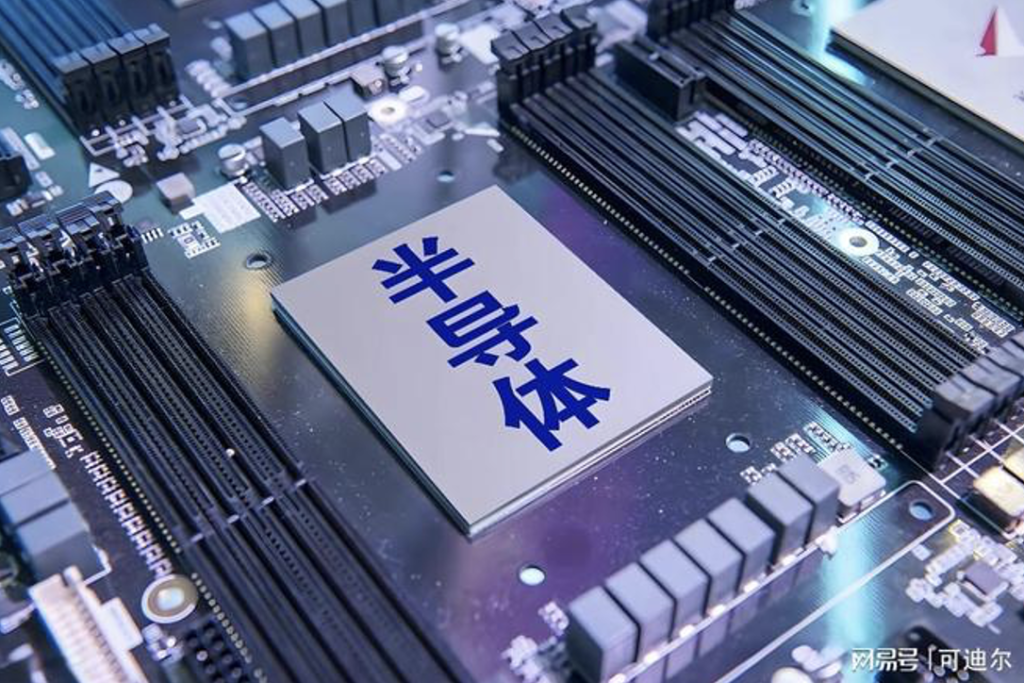